The GreenH2ICE project aims to investigate and develop an integrated, high-efficiency renewable hydrogen production station for vehicle fuelling, in particular through the design of an electrolyser and a new process for converting internal combustion engines to run on H2 (watch the video). The project started in March 2018 and has the participation of the National Laboratory for Energy and Geology (LNEG). This is a project co-financed by Portugal2020. Know more details about the co-financed project.
PROJECT GOALS
Study, design and construction of a hydrogen production system and respective storage.
Conception, design and construction of the prototype of a high performance alkaline electrolyser.
Pioneering exploratory integration and combination for safe, environmentally and economically viable production, storage and dispensing of hydrogen.
Conversion from internal combustion automobile engine to hydrogen.
Monitor and manage the hydrogen production, storage and distribution process using industry 4.0 technologies.
WHY THE HYDROGEN?
Over the past 20 years, several stakeholders have worked together to look for sustainable alternatives to the use of coal, gasoline, diesel, and natural gas.
The use of hydrogen-powered vehicles emerges as a credible alternative in terms of autonomy, and in terms of circular economy, as the engines existing in today’s cars can be operated either with hydrogen or gasoline, not requiring high hydrogen purity (as opposed to fuel cells). Otto engines, when powered by hydrogen, are cheap and reliable, emitting practically 0% CO2.
Interest in hydrogen as an alternative transport fuel comes from:
- the ability of internal combustion engines to operate without CO2 emissions, matching fuel cells and electric vehicles with zero emissions;
- potential for domestic production;
- fast filling time;
- high efficiency of hydrogen engine, comparable with fuel cell efficiency.
Emission Factores
Net Calorific Value
However, despite the abundance of hydrogen in nature, one of the biggest challenges to its use lies in its efficient obtainment, as well as its storage.
H2 PRODUCTION
Hydrogen can be produced from a variety of raw materials. These include fossil resources such as natural gas and coal, as well as renewable resources such as biomass and water, using renewable energy sources.
To this end, various chemical, biological, electrolyte, photolytic and thermochemical technologies can be used, each of which has advantages and disadvantages and a different maturity stage.
In absolute terms, 14 different processes have been identified that allow the production of hydrogen. In the GreenH2ICE project, alkaline water electrolysis was the selected process.
High-Pressure Alkaline Electrolysis
The electrolysis of water consists of the decomposition of the water molecule into hydrogen and oxygen through the use of electrical energy. It is a non-spontaneous endothermic process, hence it is necessary to supply electrical energy for the reaction to occur.
A high-temperature electrolysis process may therefore be preferable when heat is available as waste heat from other processes. This data is especially important worldwide, as most of the electricity produced is based on fossil energy sources with relatively low efficiencies. In procedural terms, the electrolysis of water can be carried out using seven processes:
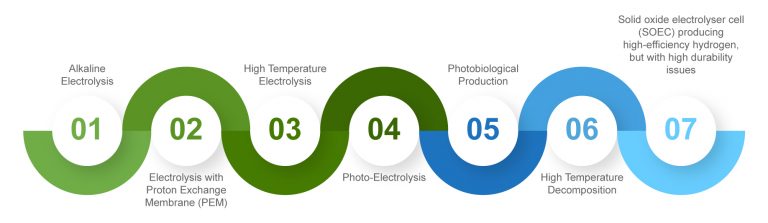
In the GreenH2ICE project, a high-pressure alkaline electrolyser was developed. In these electrolysers, water is decomposed, separating hydrogen and oxygen through a membrane.
Alkaline electrolysis provides a sustainable solution for hydrogen production and is suitable for coupling with renewable energy sources such as wind and solar energy.
PROJECT INNOVATIONS
- Resource to turbulence, in its chambers;
- Pulsed feeding;
- High efficiency and resistance membranes;
- Electrodes with catalytic coatings.
- Multipoint-port injection electronic injection solution;
- Direct injection solution for high performance;
- Interchangeable bottle fill solution/liquid organic hydrogen car LOHC.
- Compliance with European Union vehicle safety rules.
- hydrogen does not need to be of high purity which reduces the cost of its production by about 25%.
- its efficiency at high loads increases substantially and NOx emissions are only felt in very rich mixtures.
- the converted vehicle can also work on petrol or diesel, without limiting its autonomy.
- Converting a combustion engine vehicle to run on hydrogen is an excellent example of Circular Economy, given that 70% of a car’s lifetime emissions take place during its manufacturing process.
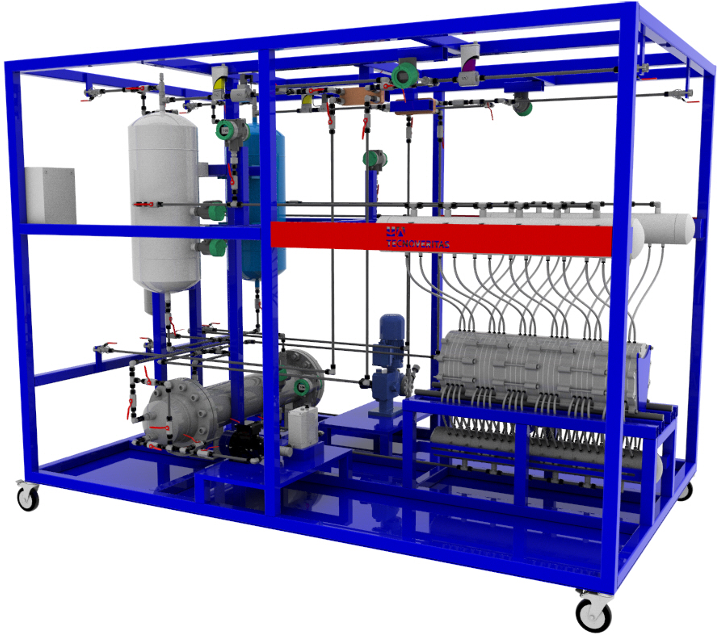
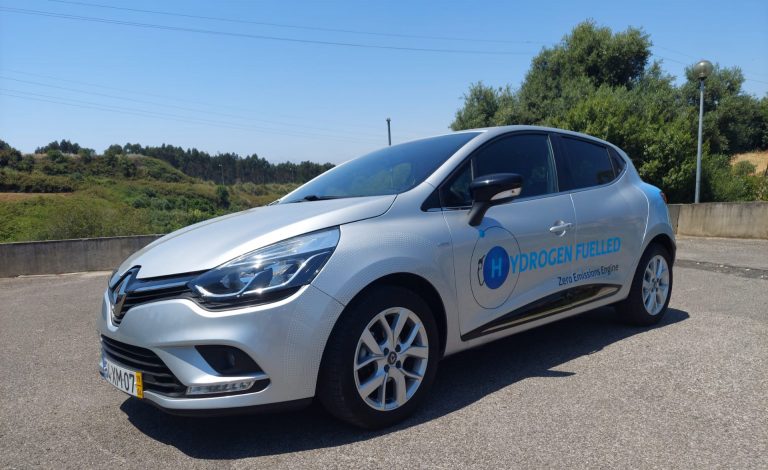